A car’s performance is said to be defined by its movement—run fast, run strong. But in recent years, several new standards have been added to complement these criteria, including eco-friendliness and fuel economy. Car manufacturers have also become more sensitive to drivers’ individual preferences, so that ride comfort and shifting ‘feel’ have become fairly commonplace criteria for choosing cars as well.
Hyundai Motor Group has always strived to do its best in the R&D of powertrains, the essential foundation for a car’s performance and efficiency. But with changing times demanding more variegated approaches to powertrain design, the Group, too, has expanded its focus to developing powertrains that 1) better respond to drivers’ sentiments and preferences, 2) contain engines and transmissions that more nimbly respond to the driver’s maneuvers, and 3) still manage to function harmoniously with the vehicle at large.
Smart + Stream
Smartstream is the next-gen brand name for the powertrain line that embodies Hyundai Motor Group’s efforts to lead the world’s next generation of mobility. It responds to various and divergent needs of modern drivers, preparing for the coming years in which HEVs (Hybrid-Electric Vehicles) and PHEVs (Plug-in Hybrid Electric Vehicles) will become mainstream. Because both still require the traditional internal combustion engine (ICE), Smartstream R&D also includes continued efforts at polishing the existing technologies for ICEVs as well.
But given that ICE technologies are already at or near the apex point, an addition of one or few cutting-edge technologies cannot produce drastic performance improvements or the disruptive changes demanded by consumers. So we started from scratch—starting from the smallest unit of parts, rethinking the engine specs and design. Large changes, we believed, could come from a collection of small improvements.
The finished Smartstream lives up to our high expectations: the ‘Smart’ technological objectives of saving fuel, improving performance, and reducing gas emissions were applied to every step of the ‘Stream,’ the stream of air and fuel injected in the engine, its explosive power delivered to the wheels via the transmission. This is the stream that you too will follow, as we review Smartstream’s core technologies below.
Continuously Variable Valve Duration (CVVD)
In a gasoline engine, the most important aspect of producing power is in controlling the amount of air intake. Of course, it is the meeting of the air and the fuel that creates the explosion that leads to power generation. But as the amount of fuel injection is determined by the amount of air intake, controlling the air is the prerequisite to matching the precise intention of the driver who presses the gas pedal.
Picture, for a moment, the engine interior. The pistons and the valves interact, in a routine by which the engine inhaling air, compresses it, gets it to combust, and lets out the exhaust gas. Within this so-called four-stroke cycle (intake, compression, combustion, exhaustion), the valves—both the intake valve and the exhaust valve—serve as the doors that let the air in and out.
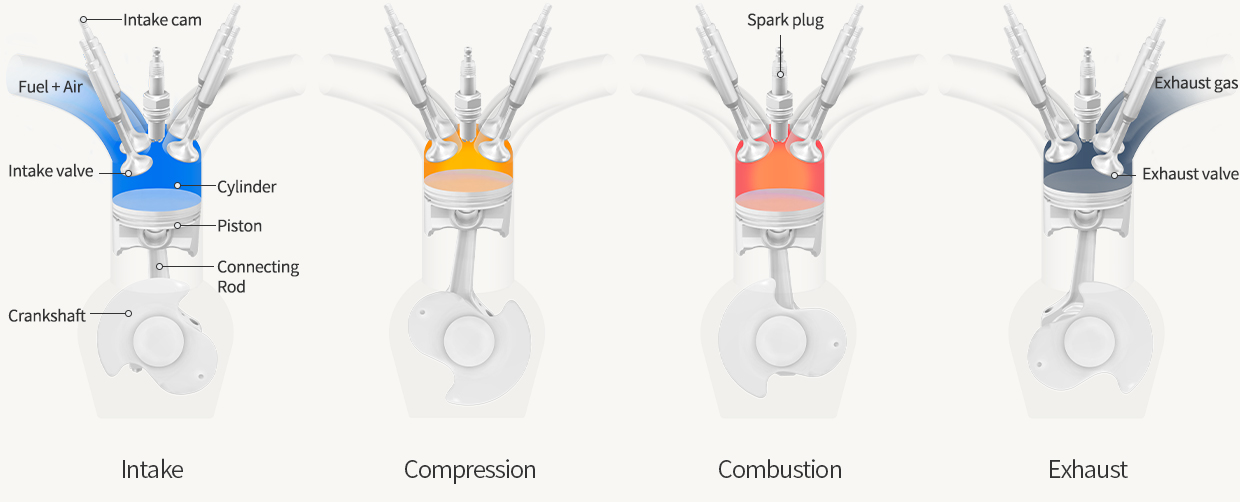
But of the four strokes in the cycle, the only step that produces actual power is the combustion stroke. The remaining three strokes, in fact, require power for taking in, compressing, and releasing air; meaning, prolonging these processes represents a power loss for the engine. That’s why the timing of the valve’s opening and closing—taking in just the right amount of air to maximize the combustion and minimize the energy loss—becomes crucial.
The ‘valve overlap’ concept comes into play here. It may seem that during the intake stroke, one would need to close the exhaust valve. But in reality, leaving the exhaust valve open for a short duration at the beginning of the intake phase facilitates the process by having the exhaust gas “inhales” the fresh air as it is released; the incoming gas also serves to “push out” the exhaust gas toward the exhaust valve, thus minimizing the undesirable exhaust remnants. But given that there are many variables (vehicle speed and engine load, for example) that determine the optimal valve timing, for long it was impossible to put this concept into flawless action.
The breakthrough came with Porsche’s Variocam in 1992—nearly a century after the development of the first engine. Since then, countless variable valve technologies have emerged. Most car manufacturers nowadays use the global standard technology CVVT (Continuously Variable Valve Timing) to continuously vary the time of the valves’ opening and closing to maintain the optimum point.
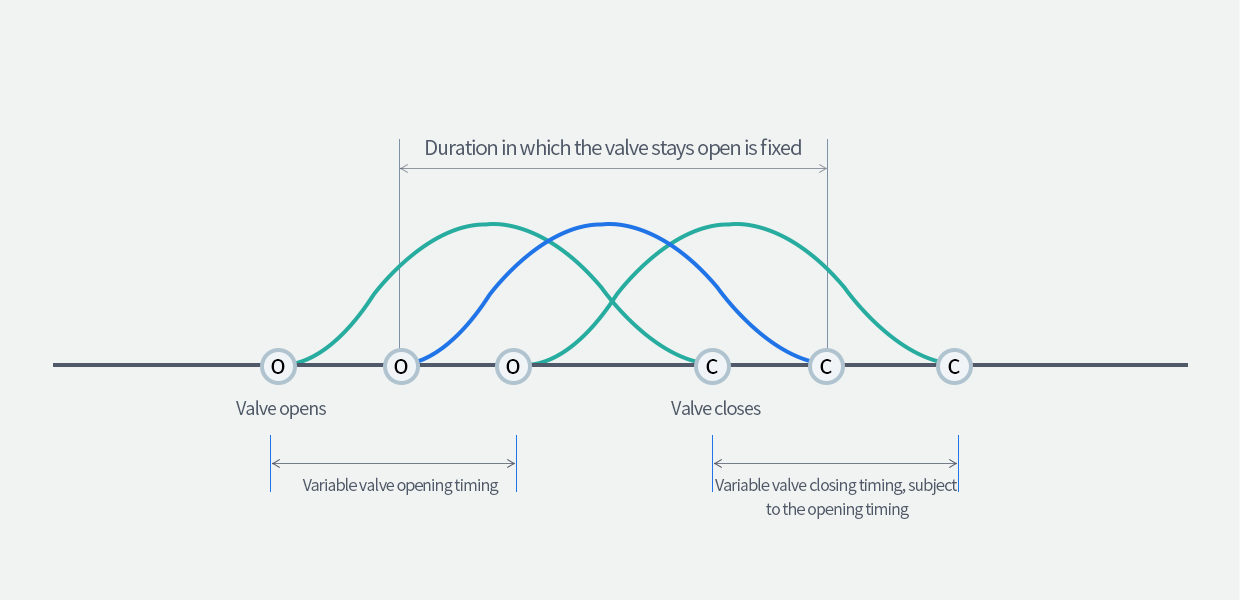
But even CVVT has its limits. Under the CVVT scheme, the cam’s iterating movements forward and backward determines the duration through which the valve stays open. But because the cam’s shape is fixed, it is impossible to change this duration. If you open the valve early, then the cam inevitably closes it early; open it late, the valve will close late. The modern engines with CVVT thus molded the cam to pre-fit the purpose of the engine—prioritizing performance, or fuel economy, or some compromise between the two.
CVVD was Hyundai Motor Group’s answer to this dilemma. Without changing the shape of the cam, the Group has utilized time divergence as inspiration for the solution. Putting it simply, under the CVVD scheme, the speed of the cam passing by the valve determines how long the valve stays open. A slow-passing cam keeps the valve open for a longer duration, while a fast-passing one keeps the valve open for only a short duration.
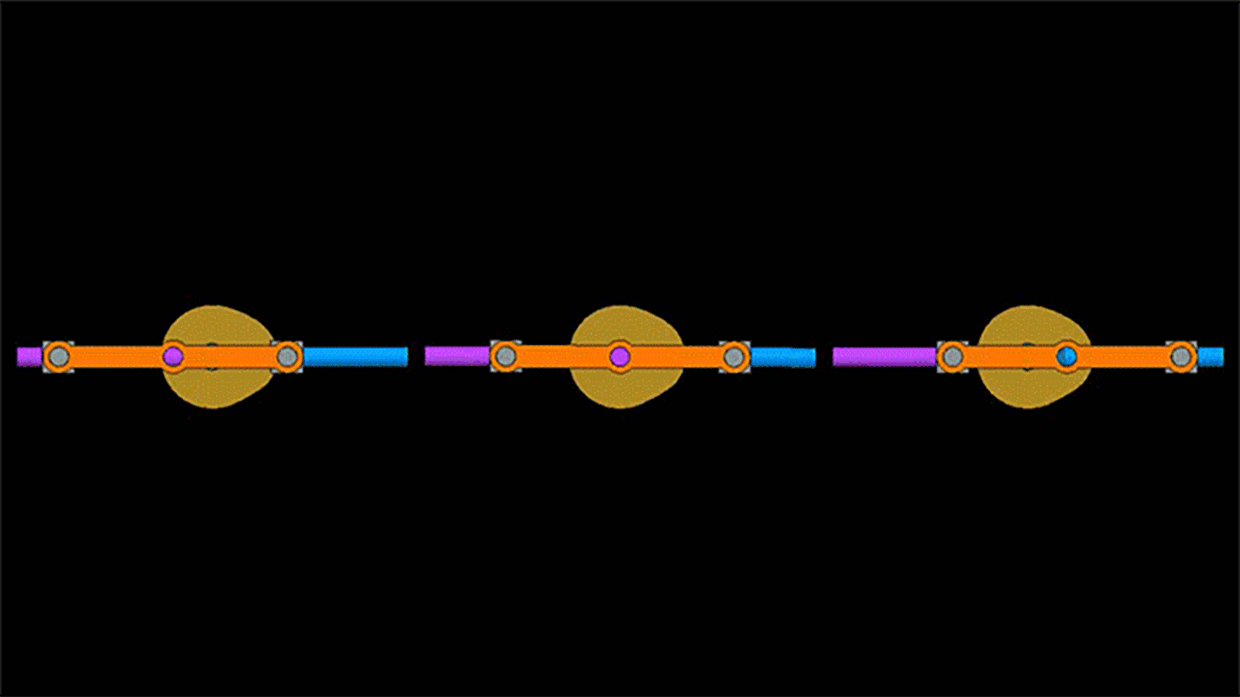
When combined with CVVT, CVVD can vary the duration through which the valve stays open. A valve that opens early can stay open for long by having the cam pass slowly in the first place; a valve that opens late can shut early by having the cam pass quickly.
To explain the mechanism in terms of the four-stroke cycle: during a normal drive, after the intake stroke, the intake valve stays open well until the mid/end phase of the compression stroke, releasing the superfluous air and using just the necessary amount for the combustion stroke—in effect minimizing the piston’s compression loss. During acceleration, after the intake stroke, the intake valve is immediately shut to maximize the air intake, increasing the power generated by the combustion. In doing so, the engine showed a 4% increase in power output and a 5% increase in fuel economy over the equivalent engine without CVVD. And because the optimal valve timing after the start of the engine activates the catalyst earlier, gas emissions were also reduced by over 12%.
*Models with CVVD: Smartstream G1.6 T-GDi / G1.0 T-GDi
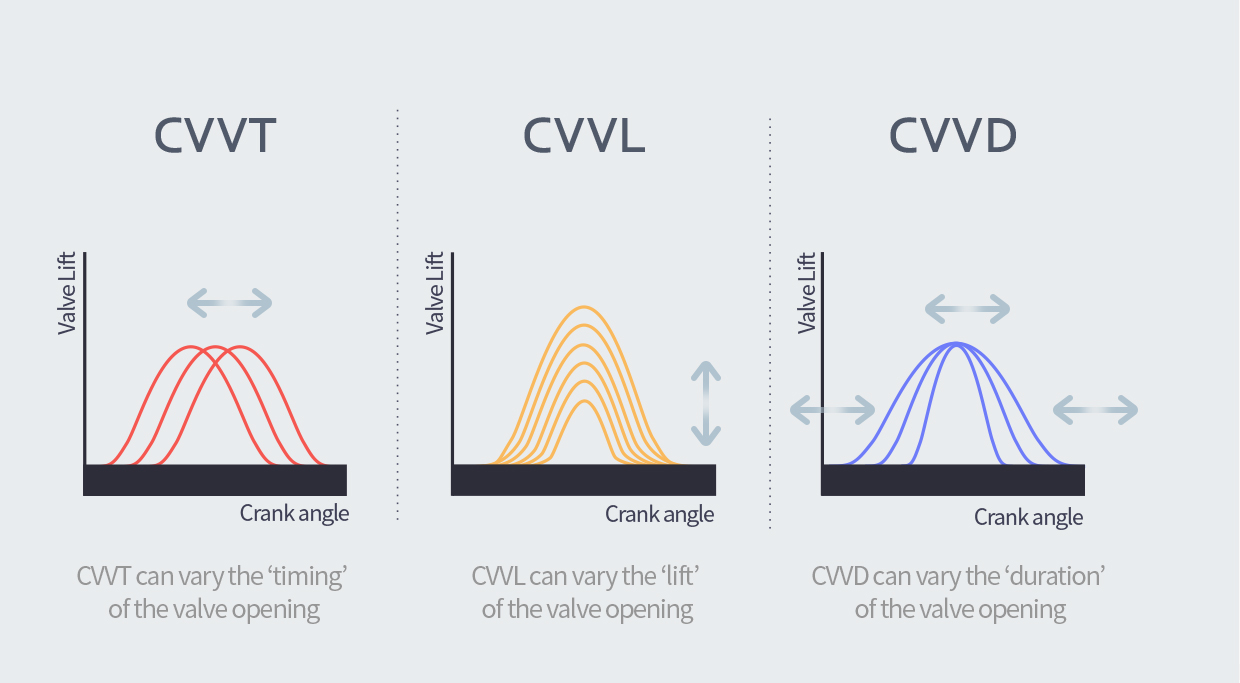
Water-cooled Intercooler
Just as controlling the air intake is important for maximizing the engine efficiency, so is increasing the compression ratio for achieving more powerful combustions. Many engines employ a turbocharger to this end: squeezing highly compressed air into the cylinder increases the engine’s power output, and this allows the engine to be replaced with a turbo engine with lower displacement for better fuel economy.
But the air compressed by a turbocharger exists at a higher temperature because its molecules collide at a higher frequency. High temperature causes the air density to fall over time, which decreases the amount of air going into the cylinder, which altogether diminishes the combustion efficiency. This is why an ‘intercooler,’ which works to cool the intake air to a suitable temperature, is necessary.
Intercoolers come in water-cooled and air-cooled varieties. Many engines use the latter, which works by sending the compressed air to the cooling fan at the front of the car and gets it cooled by the wind running outside. But this causes the compressed air to travel a long distance, which causes the so-called ‘turbo lag,’ a delay between the time the driver presses the gas pedal and the real acceleration begins. And then there is the basic limit of air-based cooling—it’s just not as effective as cooling by water.
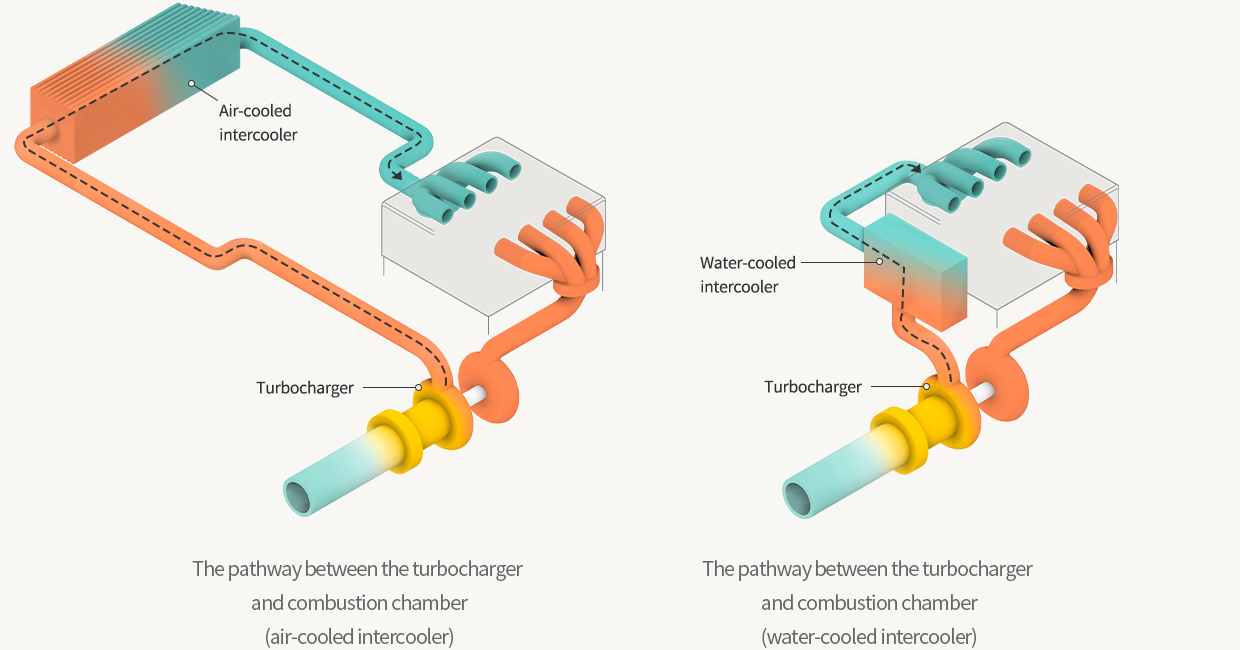
Water-cooled intercoolers, on the other hand, place the intercooler right next to the engine, shortening the distance the compressed air needs to travel. The turbocharged air is delivered quickly to the cylinder, making the engine more responsive. And of course, it uses water to cool, as the name suggests—and its superior cooling performance allows stable acceleration even in steaming summers or air-thin high altitudes.
*Models with water-cooled intercoolers: Smartstream G2.5 FR T-GDi / G3.5 FR T-GDi
Dual-Port Fuel Injection (DPFI)
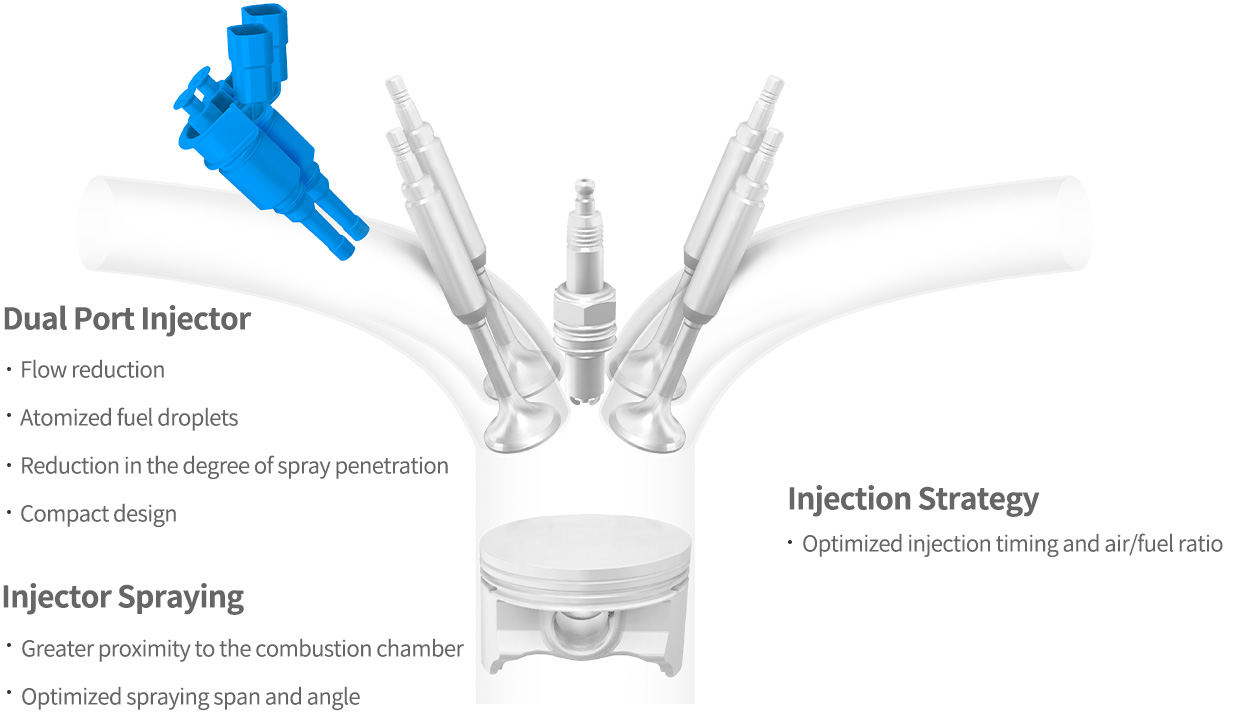
With the valve control and the intercooler having done their jobs, the next step is to inject fuel. The important aspects of fuel injection are twofold: where to inject and how strong, and how atomized, the injection should be. The location, pressure, and pattern of injection determine the ratio by which the fuel mixes with the air; if it mixes well, its stable combustion can improve fuel economy and reduce the emission of harmful gases. To this end, Hyundai Motor Group has worked to discover and select the optimal injection pattern for every engine.
MPi engines structurally inject the fuel into the intake ports, so it is essential, for the sake of fuel economy and emission reduction, to minimize the amount of wall film that sticks to the ports or the combustion chamber walls.
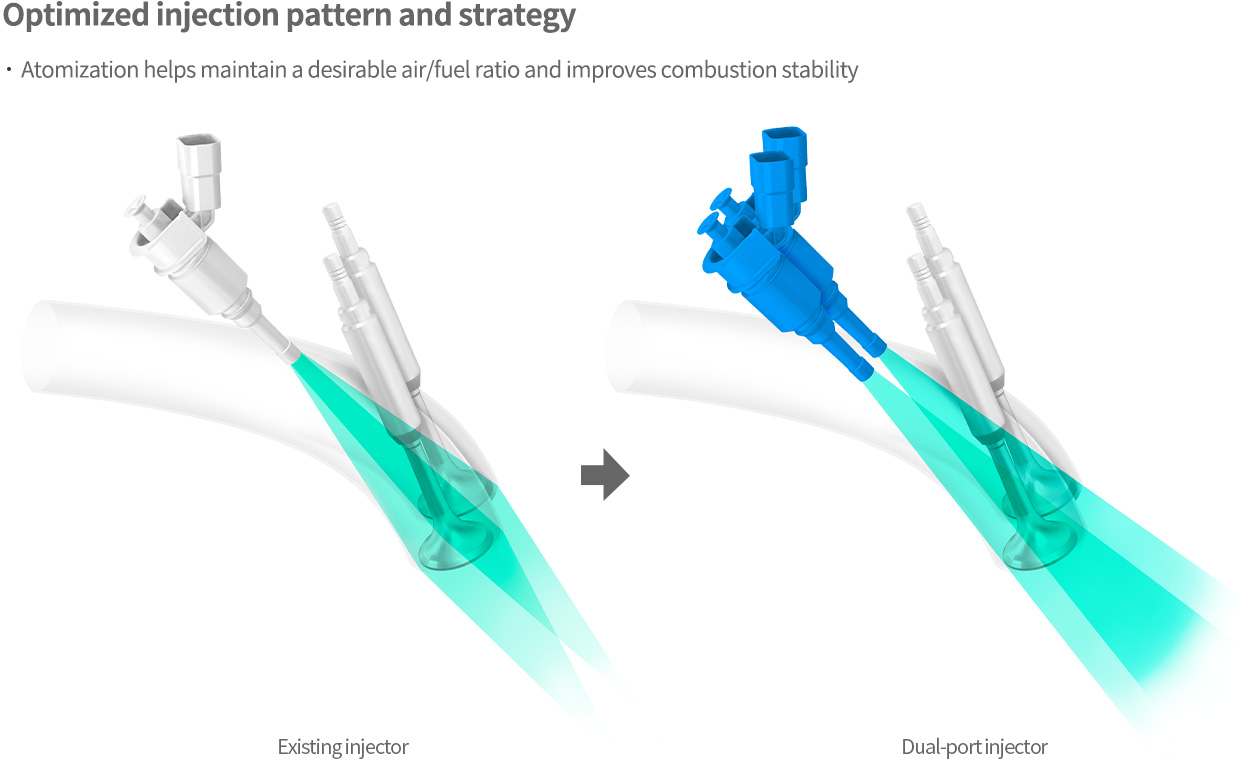
DPFI uses two injectors for each intake port to better maintain the stable air/fuel ratio in the mixer, which also improves the EGR (Exhaust Gas Recirculation) ratio, with benefits to the fuel economy. In addition, further atomization of fuel droplets mitigated spray evaporation, which reduced the emission of harmful particulate matter (PM).
*Models with DPFI: Smartstream G1.0 / G1.2 / 1.6
Dual Fuel Injection + Center Injection
GDi (Gasoline Direct injection) and MPi (Multi-Port injection) each has its pros and cons. GDi applies compressed fuel directly to the cylinder, and its precision of injection provides high power output and good fuel economy at low engine load. The cons are noise and vibration at relatively low speeds and, because the fuel might not mix well with the air, relatively high emissions of PM matter. Compared to GDi, MPi is freer from noise and vibration concerns, but it is generally worse in power output and fuel economy.
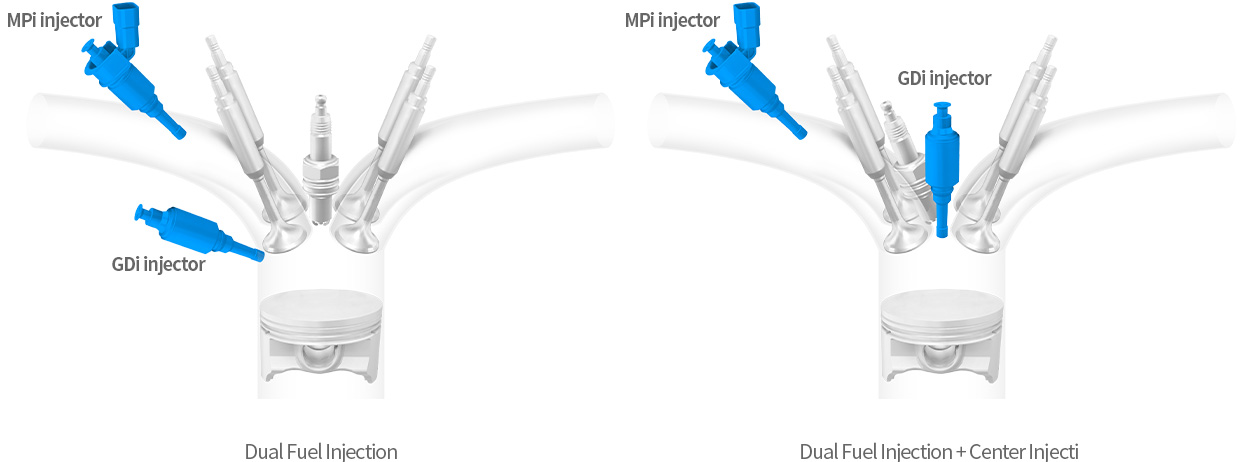
Hyundai Motor Group’s new Dual Fuel Injection system comes with two injectors, one GDi and the other MPi, for each cylinder, taking advantage of the pros of both injector types. For low-to-mid speed everyday driving, the system uses the MPi injector; for high-speed driving in highways or expressways, the system uses the GDi injector. Such optimization of fuel injection type to the driving conditions has led to an improvement in both performance and fuel economy.
Moreover, in an arrangement called Center Injection, the GDi injector has been moved to the center of the combustion chamber to produce the optimally efficient air/fuel ratio. The injector at the center is now closer to the spark plug, which allows it to particularize its injection strategies. For example, injecting a tiny amount of fuel near the spark plug right before the ignition can instantaneously facilitate the mixing of the air/fuel in the chamber and best achieve the optimal desired air/fuel ratio.
This, in turn, leads to faster combustion that contributes to improved performance and fuel economy. Finally, the injector being placed at the center better allows for symmetrical injection patterns that help reduce the amount of wall wetting (the phenomenon in which the fuel adheres to the chamber walls).
*Models with Dual Fuel Injection: Smartstream G2.5 GDi / T-GDi
*Models with Dual Fuel Injection + Center Injection: Smartstream G3.5 GDi / T-GDi
High Tumble Combustion System (HTCS)
Faster combustion speeds require good mixing of air and fuel. And good mixing requires the formation of appropriate vortexes—like swirl or tumble—that facilitate the mixing. By tailoring the intake port and the piston bowl design to maximize the tumble ratio, the HTCS works to deliver as much power generated by the combustion as possible to the pistons. To this end, Hyundai Motor Group has redesigned the engine specifications from scratch, improving combustion stability and maximizing the engine efficiency.
*Models with HTCS: Smartstream 1.6 / 1.6 T-GDi / 2.0 GDi HEV / 2.0 T-GDi
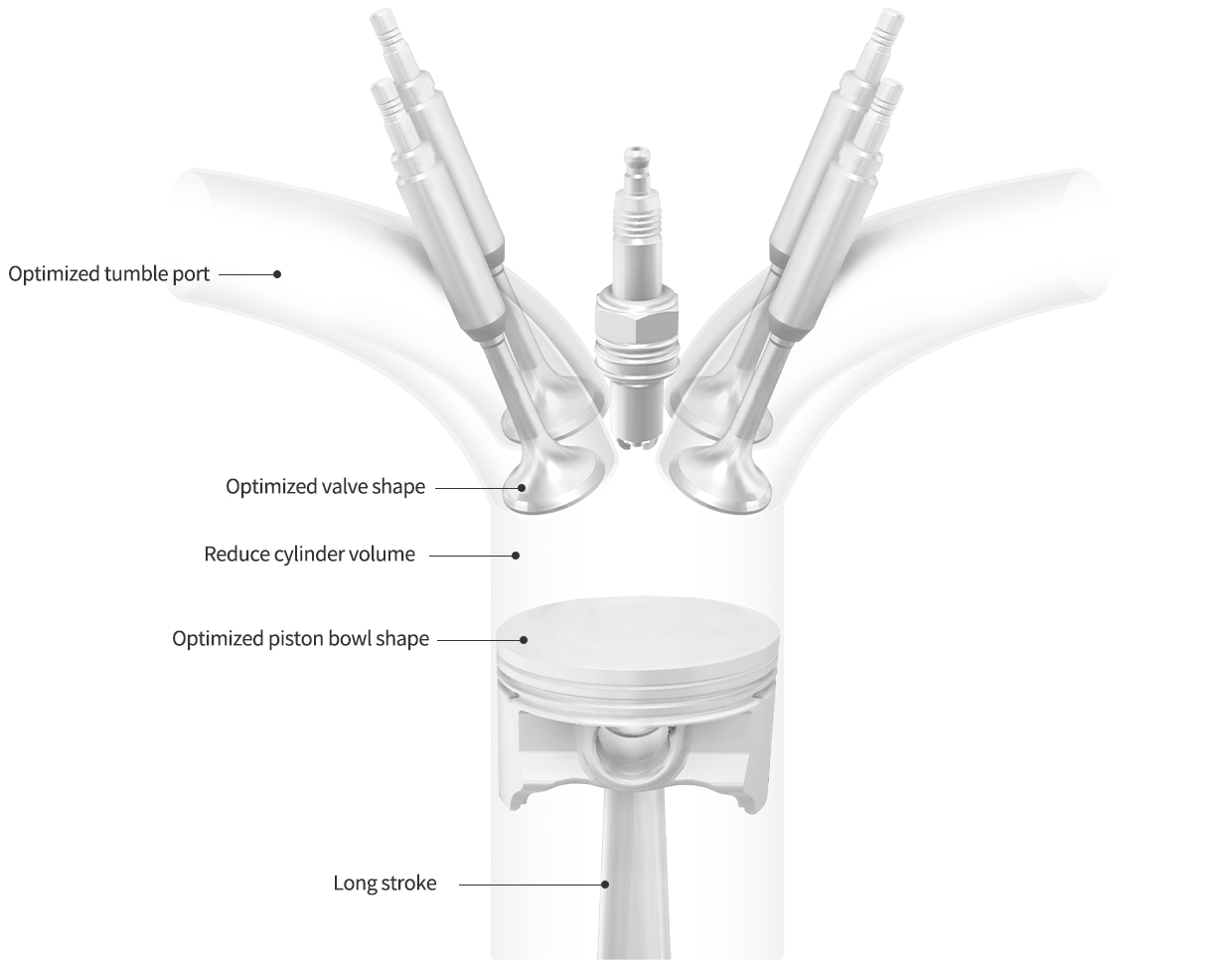
Integrated Thermal Management System (ITMS)
Another important factor for engine efficiency is the management of the environment in which the combustion occurs—that is, the thermal conditions of the engine itself. Hyundai Motor Group’s answer to this factor is the Integrated Thermal Management System (ITMS), which not only regulates engine temperature but also controls the vehicle’s heating and air conditioning. ITMS places next to the engine a 3-way valve that regulates the flow of the engine coolant to the radiator, transmission oil warmer, and heater. The valve can not only open and shut but also control the amount of coolant flow, making it a control tower that sets the overall coolant flow pattern that suits the engine’s status.
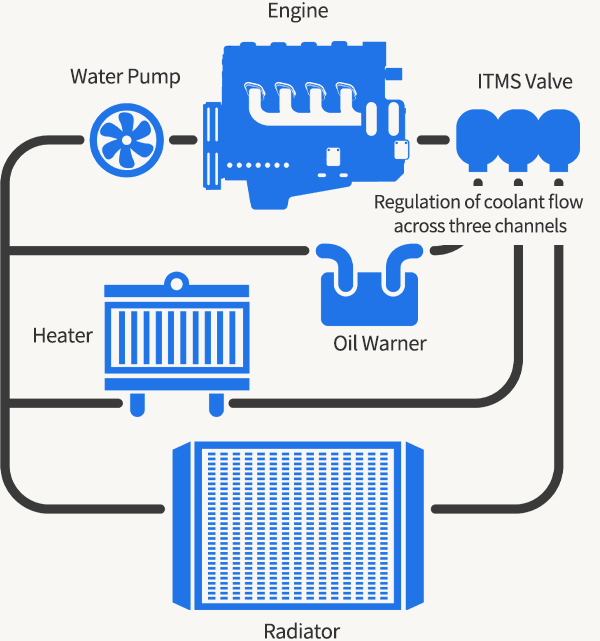
For example, when a car starts, all valve channels are shut to prevent the dissipation of heat, and this quickly raises the engine temperature. This way, the engine arrives sooner at the temperature at which the engine oil’s viscosity is at the optimal point, with the reduced friction contributing to fuel economy. In another situation, the car may be traveling at high speeds, burdening the engine with large loads and even causing an engine knock. In this case, the valves work to quickly dissipate the heat and lower the engine temperature, alleviating the knocking issue and again improving fuel economy.
ITMS is not just about regulating engine temperature, though; as already established, it can also regulate the coolant flow to the heater according to the driving conditions and the driver’s intent, improving the heating and air conditioning performance as well as efficiency.
*Models with ITMS: All Smartstream models
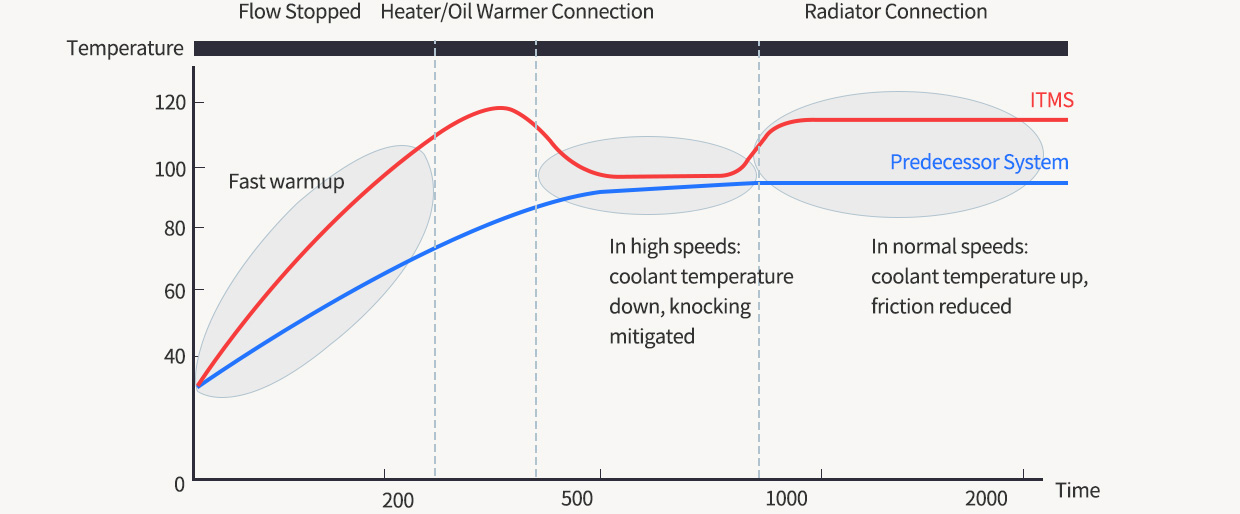
Friction-Optimized Moving System (FOMS)
Managing the thermal conditions of the engine is important for efficiency’s sake, but more fundamental to that objective is designing an engine that minimizes friction. The engine is made up of countless interlocking mechanical parts, many of which are moving parts essential to the very function of generating power.
These moving parts inevitably undergo friction upon every movement cycle. And the friction here is not just an intriguing physical phenomenon; it has ramifications to nearly all commercially important aspects of the engine, including fuel economy, performance, and durability. Friction also causes heat, which reduces energy efficiency, not to mention noise and vibrations that impact ride comfort.
Maximizing the engine’s fuel economy therefore requires technology for reducing friction. Hyundai Motor Group’s Friction-Optimized Moving System (FOMS) uses cutting-edge lightweight material and coating technologies to dramatically reduce the friction coefficient. With FOMS, the friction in the engine has reduced by 34%, helping to minimize energy loss and to improve fuel economy.
*Models with FOMS: All Smartstream models
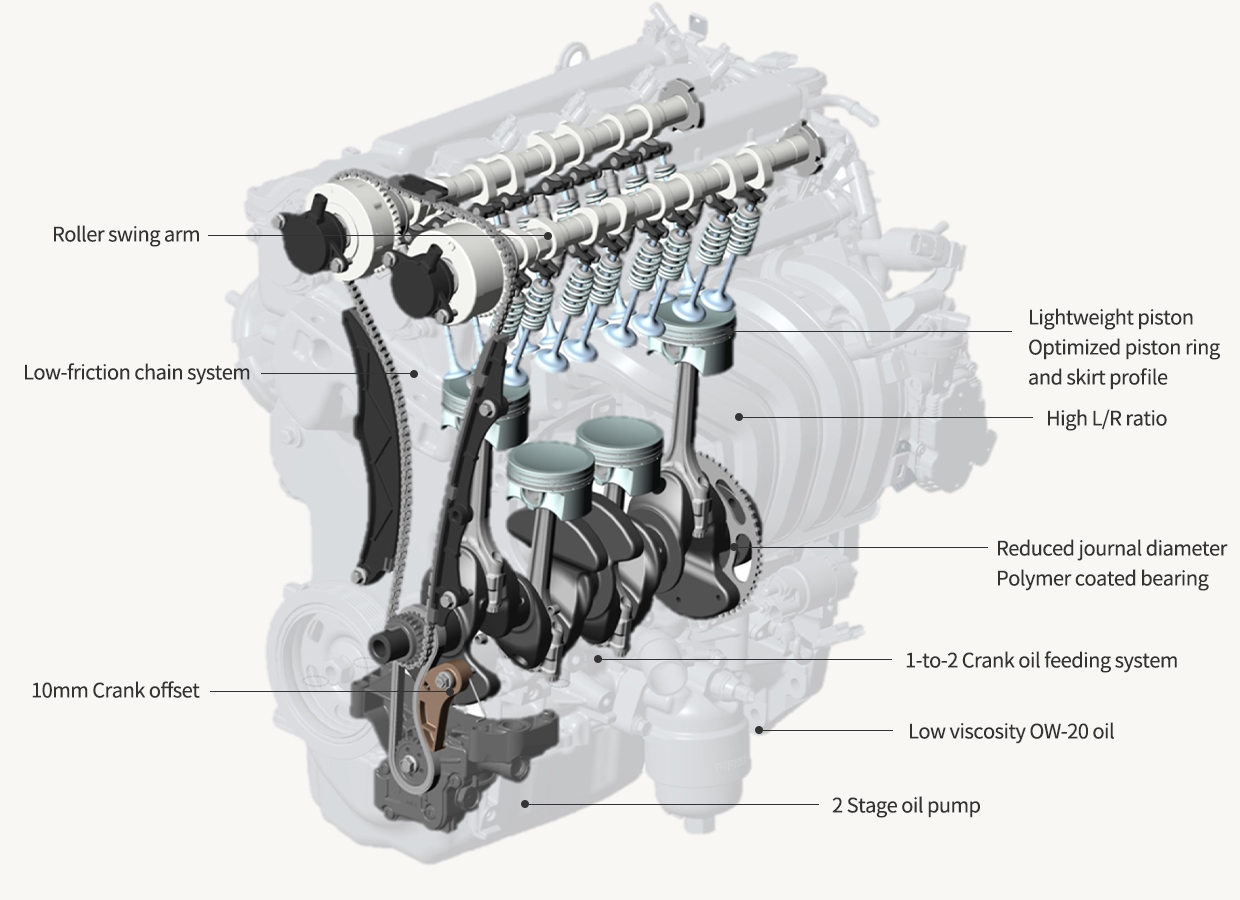
High-Ignition Energy EGR
Another important virtue of a good engine is minimizing exhaust gas. The exhaust gas includes high levels of Nitrogen Oxide (NOx) when the combustion environment is high-temperature. EGR (Exhaust Gas Recirculation) recirculates some of the exhaust gas back to the engine, thus reducing the temperature in the combustion chamber and, consequently, the NOx emissions.
Smartstream’s High-Ignition Energy EGR (HIE-EGR) improves the performance of EGR by adding a high-capacity external EGR cooler and high-energy ignition coils (with the ignition energy increase from 50 to 120 mJ), which together secure stable combustion even when the EGR ratio increases. The changes have the effect of not only reducing NOx emissions but also alleviating engine knocking and reducing pumping loss, improving the fuel economy of the engine. And because the choice of the high-energy ignition coils have allowed an expansion of the range of high EGR ratio area, the resulting increase in EGR flow has improved the engine’s fuel economy by 2 to 5 percent, dependent on the driving mode.
Hyundai Motor Group’s HIE-EGR System is adapted to two engine types, regular and turbo. The regular engine comes with the Cooled EGR System, whereas the turbo engine employs the Low-Pressure (LP) EGR System, which mixes the exhaust gas that has passed the catalyst with fresh air at the front end of the turbocharger compressor. This arrangement focuses on alleviating engine knocks as well as reducing the exhaust gas temperature for fuel economy’s sake.
*Models with HIE-EGR: different versions of the system were applied, dependent on the target engine’s characteristics.
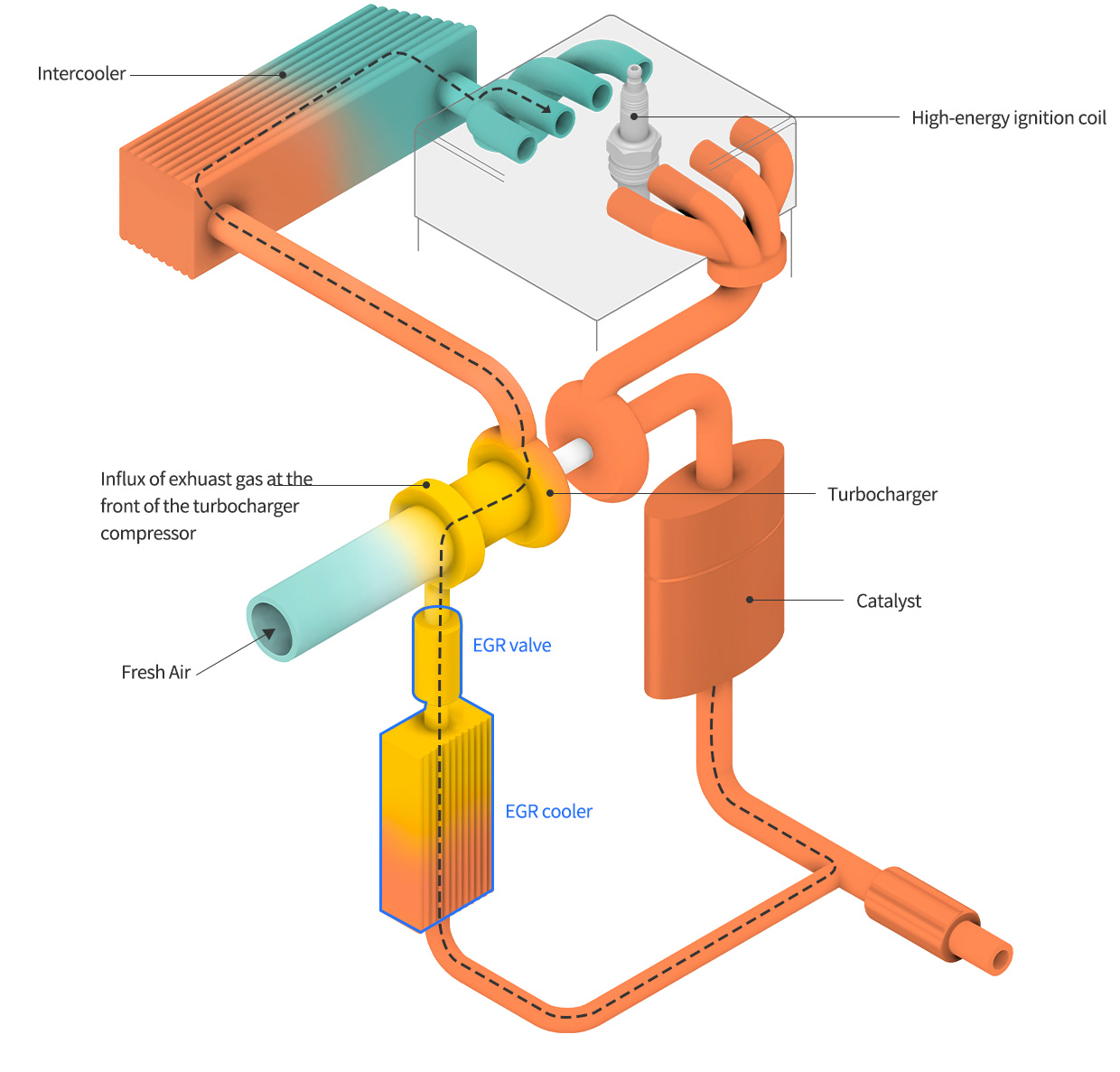
Smartstream IVT
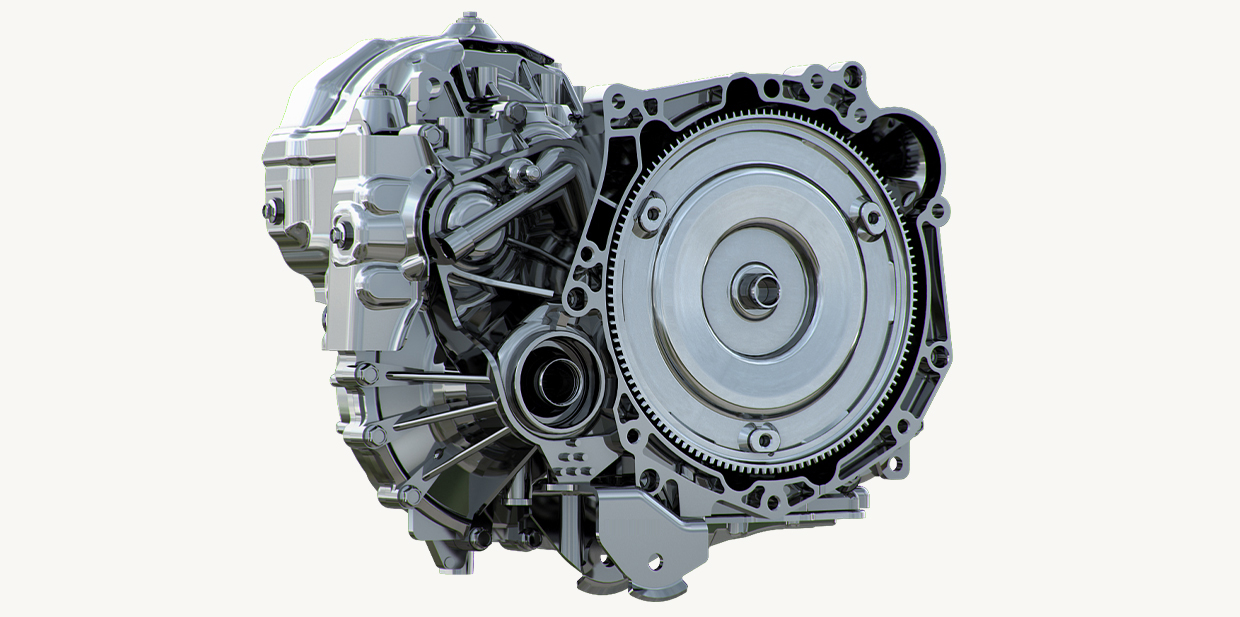
In internal combustion engine vehicles (ICEVs), the transmission serves an important role of situationally adjusting the engine RPM to allow controlled application of power. Appropriate shifting of gears can let the engine to continuously function at the desired range of high-efficiency, improving both performance and fuel economy. Recently, auto consumers have developed divergent preferences for vehicles with distinct acceleration performance and shifting ‘feel,’ and a variety of transmissions have emerged in the market to meet their needs. Hyundai Motor Group’s continuously variable transmission Smartstream IVT is one such entrant to the market.
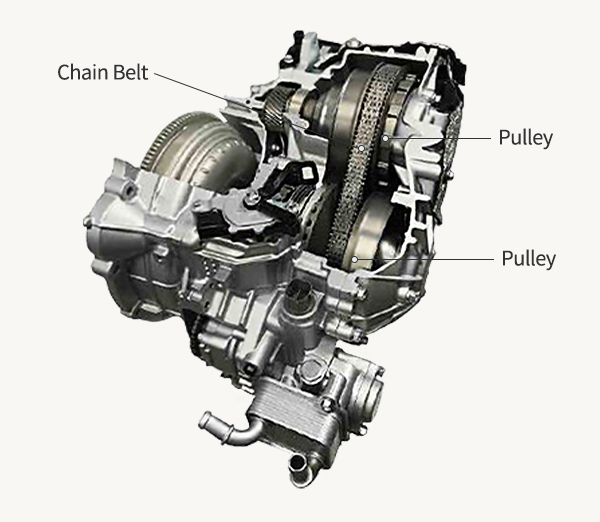
Continuously variable transmissions (CVTs) have the structure in which two pulleys connected to the engine output shaft and the driveshaft are linked via a belt. The belt contracts and expands to alter the diameter of the pulleys, thus varying the gear ratio. Because they can continuously vary the gear speed, even from the lowest gear to the highest gear, CVTs is capable of setting the optimal engine RPM for maximal power output and efficiency.
In fact, thanks to this structure (as distinguished from standard 8-speed ATs), CVTs can theoretically set the optimum gear ratio down to the decimal point within the available range. As a result, they boast a 20 to 30% improvement in fuel economy over regular transmissions, not to mention allowing for a smooth ride without clunking from the shifting. This smoothness, though, is often misinterpreted by some drivers as “low in power,” and some even go further to state that it lacks of “driving fun that comes from shifting.” What’s more, there were some mechanical difficulties in the early versions as well: the belt could not withstand the engine’s power output for too long, causing durability issues. In other instances, the pulleys and the belt often slipped against each other, causing unwanted noise and worsened fuel economy.
Hyundai Motor Group’s Smartstream IVT is the next generation of CVT that has maximized its advantages and addressed the durability and ‘feel’ issues that plagued the original. It approximates the shifting feel of regular ATs by creating virtual shifting patterns that respond to the driver’s intent. In essence, the IVT is the CVT with virtual gear speeds—and it is an answer to those who found the CVT uninteresting to drive.
Moreover, the IVT uses not the typical metallic belt but a chain belt, the first of its kind on a similar transmission, that can better and longer withstand the power output from the engine. The chain belt, in addition, uses the belt’s tension to adjust the diameter of the pulley, a mechanism that eliminates the slippage that had been the cause of the noise and the fuel economy loss.
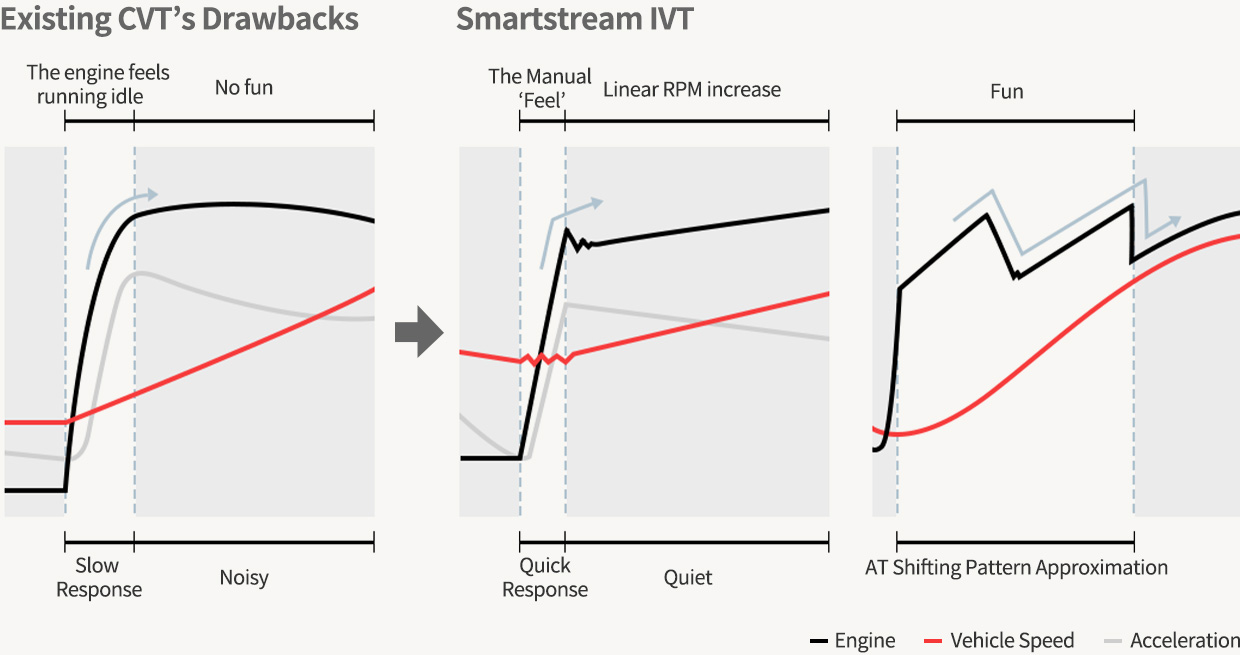
Smartstream Wet 8DCT
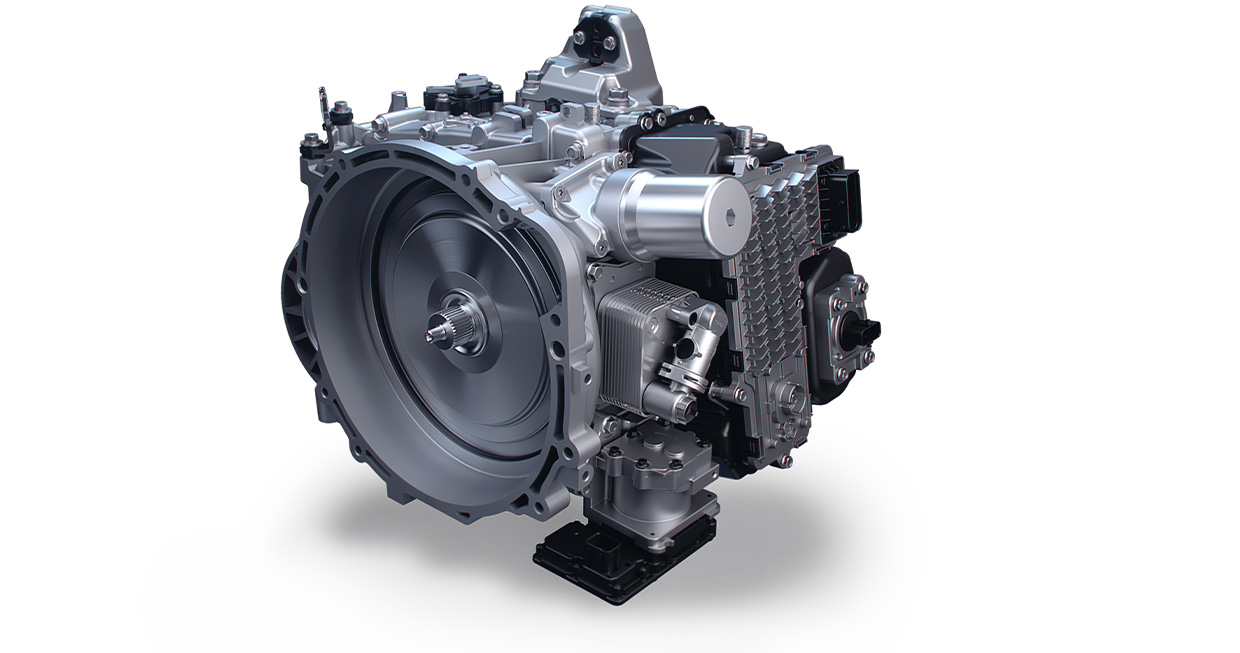
The Dual-Clutch Transmission (DCT) combines the advantages of manual transmission (MT) and automatic transmission (AT). DCT’s fast shifting and highly efficient power delivery supports the dynamic driving performance with the convenience of ATs, and yet it brings to the table the fuel efficiency level on par with MTs. The DCT also boasts the fastest gear-shifting duration of all transmissions because its two clutches (one for odd speeds 1, 3, and 5 and another for even speeds 2, 4, and 6) rotate in preparation for the next gear shift.
Hyundai Motor Group has long recognized the excellence of the DCT, having independently made its first DCT in 2011. The models that emphasized dynamic driving performance naturally were the first to receive the DCT, but the range of applications has quickly expanded. Select hybrid models now come with DCTs specially designed for them, and in 2020, even midsize SUVs, such as the 4th-gen Sorento, have been equipped with the new Smartstream Wet 8DCT.
Dry DCTs are structurally simple and therefore lightweight, making them efficient in both power delivery and fuel usage. But this simple structure presents fundamental limits to their cooling performance, ruling them out as an option for high-power engines. In contrast, wet DCTs use oil to cool the clutches, and are equipped with a separate electric oil pump (EOP) for this purpose. More powerful engines producing higher torques correspondingly burden the clutches more, but wet DCTs and their superior cooling mechanisms can handle the added load with relative ease.
The EOP is further composed of the High-Flow Electric Oil Pump (HF-EOP), which is responsible for gear lubrication and clutch cooling, and the High-Pressure Electric Oil Pump (HP-EOP), which supplies the oil to the accumulator and maintains the hydraulic pressure needed to control the shifting. Together, they ensure the Wet DCT’s efficient power transmission and fuel economy.
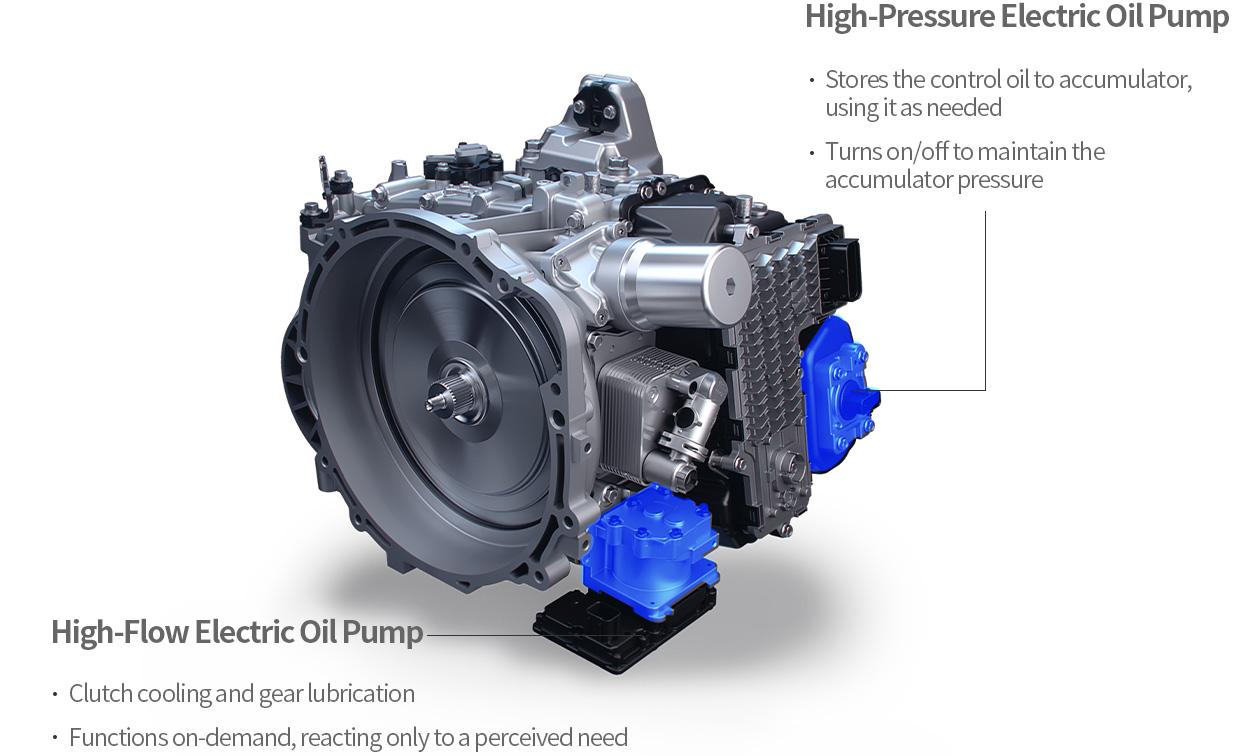
The HF-EOP functions independently from the engine RPM and pumps the coolant oil through the clutches heated by continuous shifting. More than just cooling, though, the oil serves to lubricate the gears and ensure its smooth mechanical operation. The HP-EOP functions in an on-demand scheme (activating only upon a perceived need) and maintains the level of hydraulic pressure in the accumulator, needed to control the transmission, within the acceptable range. With these two EOPs, the Smartstream Wet 8DCT has substantially reduced needless oil pump activity and consequently increased its fuel economy.
The Wet 8DCT can handle torques up to 53kgf·m, making it a possible option even for high-performance diesel engines. As a transmission that embraces the shifting mechanism of manual transmissions, it also shows meaningful improvements in such performance standards as power transmission efficiency and acceleration performance.
The Wet 8DCT’s power transmission efficiency is 93.8%, 8.7% higher than that of the existing 8AT. This higher efficiency essentially means that the power from the engine won’t be wasted. Moreover, the parts that make up the Gear Shift Cylinder (GSC; houses the valves that help control the shifting with hydraulic pressure) are now designed independently from one another, which led to an appreciable increase in shifting performance.
The advantages of Wet 8DCT are not just quantitative; there are real benefits that can be felt, tangibly, on the road. Dynamic yet smooth shifting feel provides superior ride comfort. The coolant oil keeps the clutch cool consistently, helping prevent overheating from overexertion. So the Wet 8DCT can help the car move smoothly even in conditions burdensome to the transmission, like congested roads or steep inclines.