A vehicle's platform is the key factor which decides the design, dynamic steering, safety, cabin space, and other fundamental aspects. It is no surprise that Hyundai Motors put so much resource and care into developing its 3rd-Generation Platform.
Automotive platform is a concept we hear about a lot lately. The reason is simple. A well-designed platform can lay the groundwork for various different premium cars.
Carefully planning a platform, then customizing it to best fit each model, has become standard practice in the automobile industry. Here are some reasons why it became standard practice.
First, a well-designed platform can provide a significant advantage in development costs and time. Well-tested and proven platforms and modules can be useful for multiple vehicle types, easily adjusted and configured, allowing for more efficient testing and development. Efficient use of R&D resources can create a virtuous cycle that leads to even better automobiles.
Second, a well-designed platform improves the efficiency in developing a more complete and high-quality automobile. Starting with an already excellent platform allows easier application of changes that meet specialized needs. Adjusting for completeness of design is much more economical than developing a new platform from the ground up.
Hyundai Motor Group’s 3rd-Generation Platform was created to meet those strategic objectives. The new platform is used for the 7th iteration of the AVANTE model and will be introduced to other Hyundai models. We sat down with the brilliant minds that developed the 3rd-Generation Platform. They are the researchers behind the new platform set to be Hyundai’s springboard into the future.
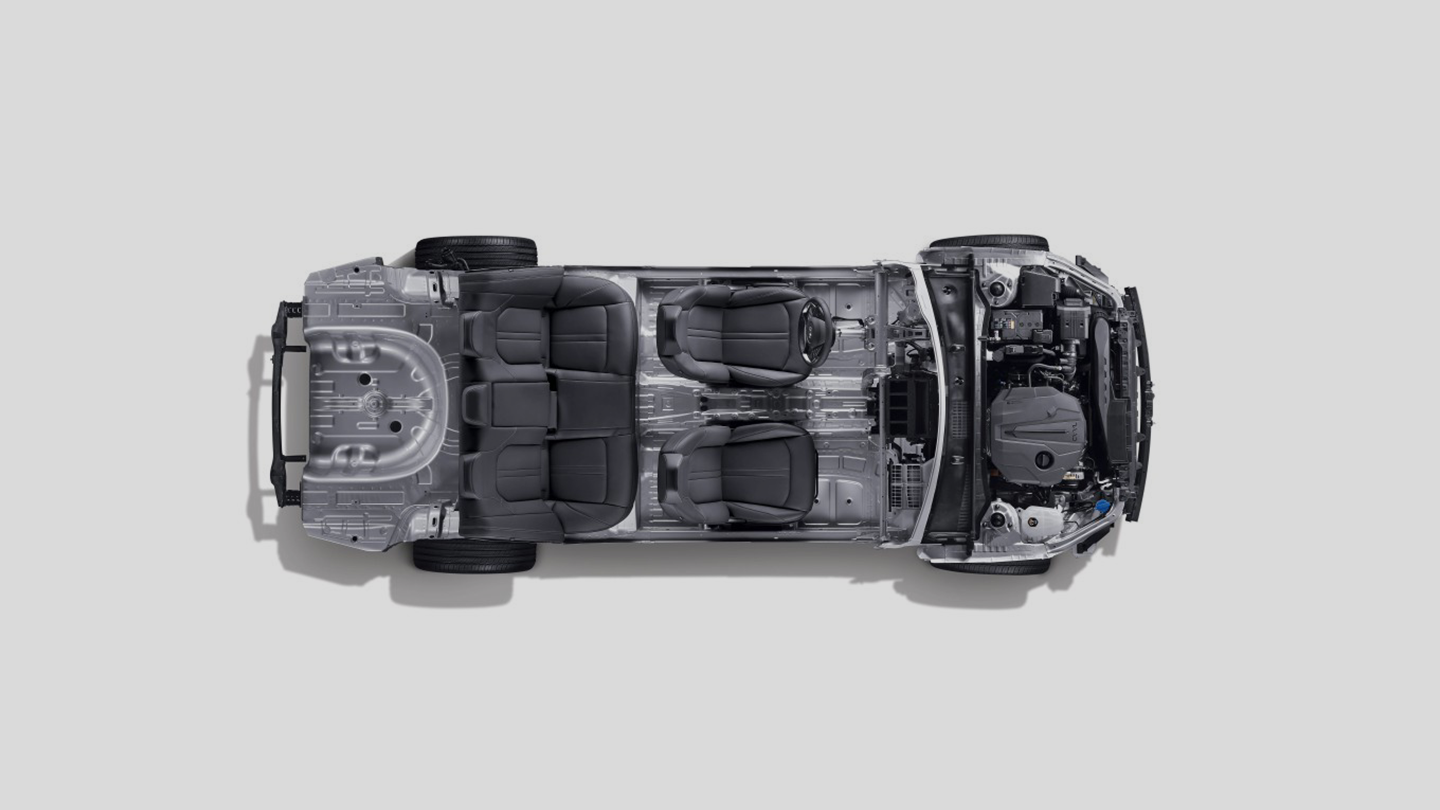
Platform can mean many different things. What does it mean in this context?
The dictionary definition for automobile platform is a compatible package of key components that includes shared design, engineering, productivity, model, and type. Considering such a wide breadth of definition, we might even say that a platform is the embodiment of the automaker’s philosophy on what automobiles are, what they can be, and how they ought to be made.
Of course, different automakers have different scopes of definition for platforms. Specifically, for the 3rd-Generation Platform of Hyundai Motor Group, the definition includes key compatible components in the undercarriage, including the underbody, suspension, power train, fuel system, air conditioning, steering, exhaust and seat frame. Generally speaking, everything in the underside of an automobile, the engine room and underbody layout is included in the platform.
Why are all the automakers trying to create a shared platform?
The platform decides an automobile’s basic performance and marketability as a product. A great deal of insight on an automaker’s capacity can be learned from how it develops and operates a platform. The more resource and time a company invests in R&D, the better the resultant automobile in terms of completeness and marketability. It allows for prioritization of resources. Additional advantages include faster time to market, economies of scale, and better basic performance. For consumers, this means better products.
Platform development also includes the concept of standardization. An automobile is a collection of tens of thousands of parts and components, each developed and tested for reliability and compatibility. Without standardization, each part and component testing will need to be done separately, increasing the amount of time and resources. The burden of increased costs is then put on the consumer. Those issues can be addressed by standardized platforms and components, where shared platforms can improve quality, consistency, and dependability. The downside of this may be that a problem found in a single component may affect multiple models, but the ability to prioritize can sufficiently correct this issue.
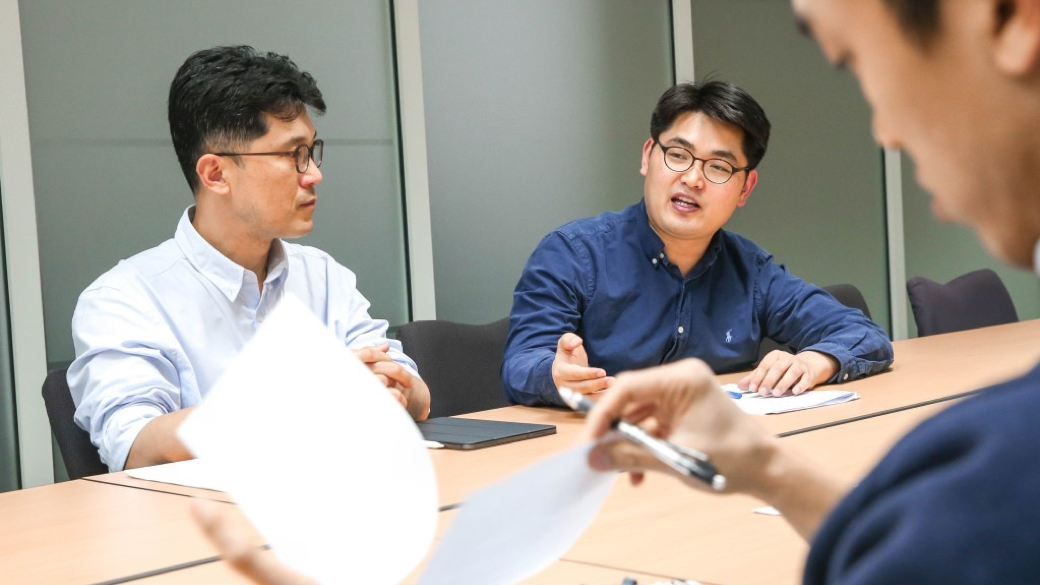
Following shared platforms, now modular platforms are becoming the norm. Could you explain modular platforms in greater detail?
A modularized platform means that the lesser parts that compose the platform are units of their own, or in modules. As the units are self-contained as modules, upgrading or switching out functions does not require an overhaul. This also means that each module option multiplies the total number of possible combinations, allowing for great diversity from a singular platform.
In theory, different modules can be put together like building blocks to make unique new cars. That is to say, modularizing components of an automobile platform is a great way to leverage shared platforms while also achieving diversification. An important consideration for bringing together modules is that the final outcome of the combination always needs to be kept in mind, to make it a complete product appealing to consumers. We created a solution for this possible challenge.
Platform modularization requires appropriate technologies for inter-component compatibility. Furthermore, it needs to be driven with a clear roadmap that portrays model-specific performance and market goals, manufacturing guidelines, cost structure, specific target market, and so on. Our 3rd-Generation Platform was developed based on that definition of modularization. Our plan is to implement the 3rd Generation designs on the 8th generation Sonata, and based on that effort, make improvements to the blueprint and implement it on future Hyundai models.
Tell us more about the development process behind the 3rd-Generation Platform. What do you start with, and in what order does the team tackle challenges?
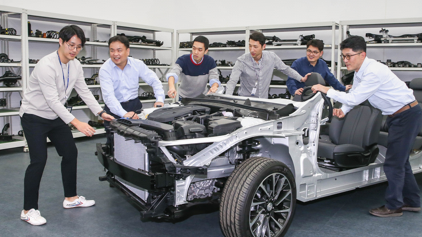
Platform development is the first step in developing a new automobile. When models are selected for mass production, the schedules are also set. Platform development precedes that selection, and also includes the legal and regulatory aspects, as well as plans to implement new technologies.
The starting point for the 3rd-Generation Platform was to prepare for the development of the multi load path structure (MLPS) chassis in anticipation of safety regulations and market trends. In the 3rd-Generation Platform development process, there were many requirements to be met at company and industry level. They included newly developed engines and decreased weight of the vehicle to reflect policies on fuel-economy, as well as collision safety standards to meet relevant regulations, as well as a need to expand on the company’s roster of eco-friendly automobiles. As a result, the development process had to account for vehicles types from sedans, SUVs, MPVs, from pre-development stages, as well as considering for the manufacturing and performance of each type.
Low profile, low-center of gravity is a key characteristic of the 3rd-Generation Platform
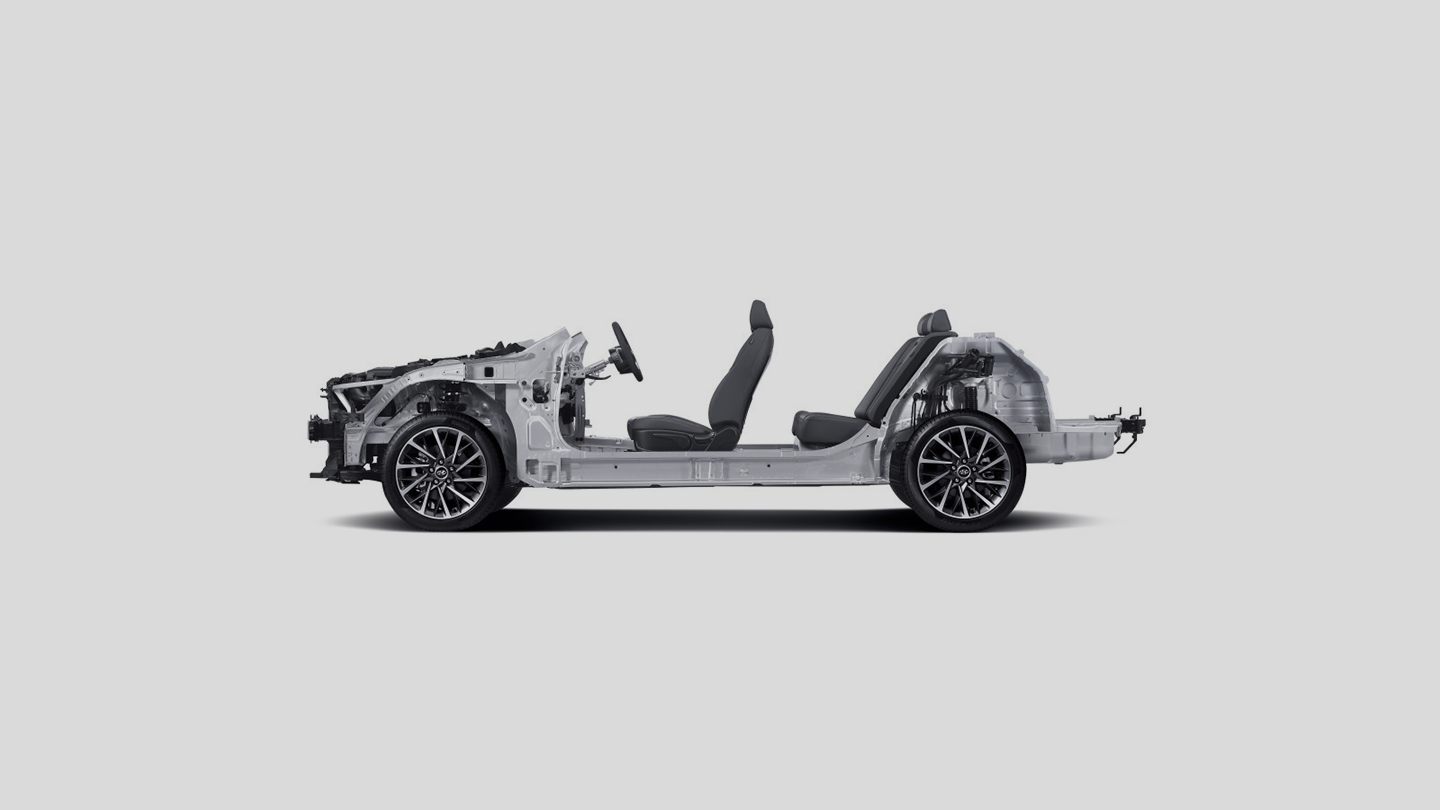
Low-profile design is a key feature in the 3rd-Generation Platform. What does that mean specifically?
A key aspect of improving driving performance and stability of a vehicle is to lower its center of gravity and to reduce the wheel’s moment of inertia, the tendency of a body to resist angular acceleration. Low-profile design addresses both those issues. Lowering the profile of a platforms sounds simple, but proper implementation is quite difficult.
It is not only about lowering the engine and drive-train, and the floor of the vehicle, but also lightening the weight of the car by placing the heavier components such as the powertrain and batteries closer to the center of gravity. It also requires a multi-faceted approach to design which takes into account safe field of view, convenient mounting and dismounting of the vehicle, and a comfortable seated and driving position. Our 3rd-Generation Platform successfully achieved all those goals, lowered the center of gravity with a low-profile, as well as making the platform more lightweight.
How was safety improved on the 3rd-Generation Platform?
Engineers approach platform safety via a three-prong approach when developing a new platform. They are energy absorption rate maximization, cabin frame preservation, and stable vehicle posture at the time of collision.
Although the second-generation platform had reached highly satisfactory levels of energy absorption maximization and cabin frame preservation, we raised the bar even further and made it competitive against even the world’s safest rated cars. However, optimizing vehicle stability in a collision scenario was not an easy challenge. It was a major focus in researching the 3rd-Generation Platform. A great deal of resources were put toward stabilizing the vehicle in a smaller overlap collision scenario.
Small overlap collisions only hit a quarter of the front of the vehicle, causing a rotation to the body of the vehicle. Greater this rotation, the greater the movement conveyed to the passengers, increasing the likelihood that the passengers are not adequately protected by safety mechanisms such as the airbag.
3rd Generation platforms include MLPS in the engine room, and subframe deformation mode control, lower arm strength and breakaway point control, A-frame deformation mode optimization that significantly decreases hazardous vehicular rotation in a small-overlap collision scenario and absorbs the collision into a relatively glancing movement. This was one way that passenger safety was significantly improved. Such a collision safety system further increases safety by significantly decreasing the likelihood of secondary accidents due to rear collisions from following automobiles on the road.
The MLPS implemented in the 3rd-Generation Platform’s engine room distributes the force of impact.
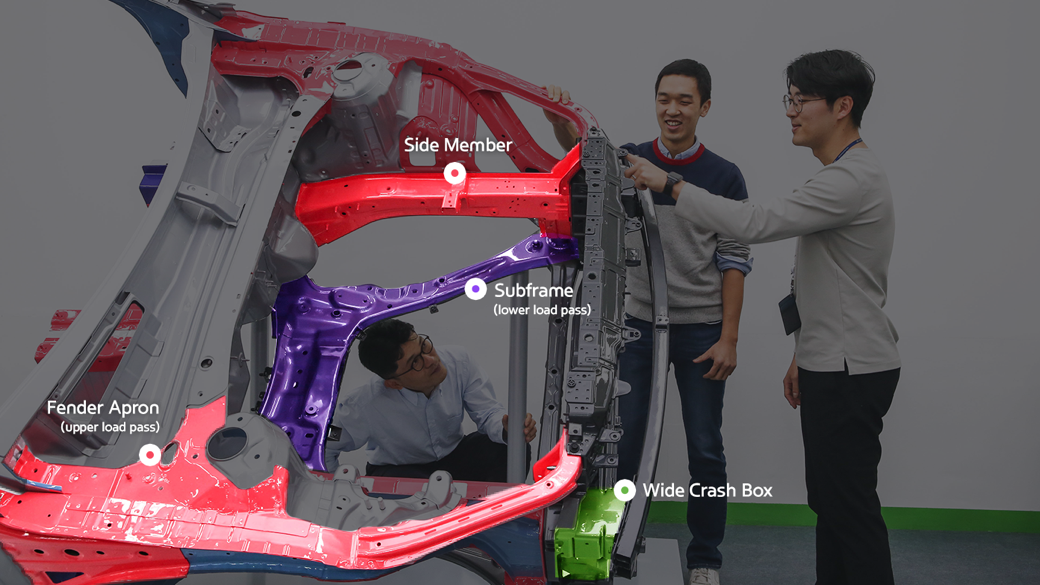
Can you tell us more about the engine-room’s Multi Load Path Structure?
Engineering researchers refer to the multi-frame engine-room structure as the Multiple Load Path Structure, or MLPS. In a typical collision situation, the side members take the brunt of the collision force. Side members are the structural supports on either side of the bonnet’s engine room. MLPS organically distributes that collision force into the front side members into the subframe, fender apron, and the overall chassis to better brace the impact, absorbing and dispersing it via various paths.
You said that the 3rd-Generation Platform was modular. Which parts or components specifically were modularized?
The underbody is the modularized part of the platform. This underbody platform is divided into four modules: front side member, dash, center floor, and rear floor. The criteria for modularizing units of the body platform module include not only the main functions of the module but also the compatibility with the car class and specifications, as well as manufacturing efficiency. For example, the rear floor module consists of components that support passenger occupancy, loading space configuration, rear impact, and noise reduction against road surface.
What are some highlights of the 3rd Generation Platform?
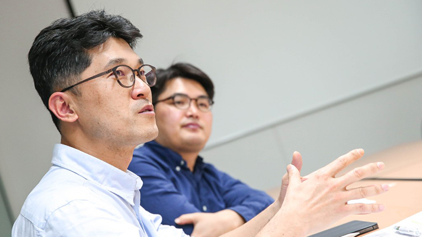
We are very proud of the autonomous function’s Redundancy System. It secures additional resources in preparation against electric or electronic system malfunctions. Specifically, the redundancies were implemented on the chassis’ steering and braking system. This includes the autonomous driving controls too.
The 3rd Generation Platform’s steering system features sensor redundancies for greater stability, and full redundancy applies from autonomous driving level 4. Hyundai Motor Group’s autonomous driving roadmap dictates double or triple redundancies for the steering system, for sensors, motor coil, ECU, power, and communications.
What was the most difficult aspect of developing the 3rd Generation Platform? It took years of burning the midnight oil, researching and testing the 3rd Generation Platform. Developing the MLPS, hybrid system, meeting design and performance specifications as well as the company’s heightened eco-friendly expectations, all those required close communications with the top brass and the hands-on team at the plant. Through that process, we were able to see our ideas and goals develop into outstanding machines competitive on the world stage, and we are very proud to put the 3rd Generation Platform out there.
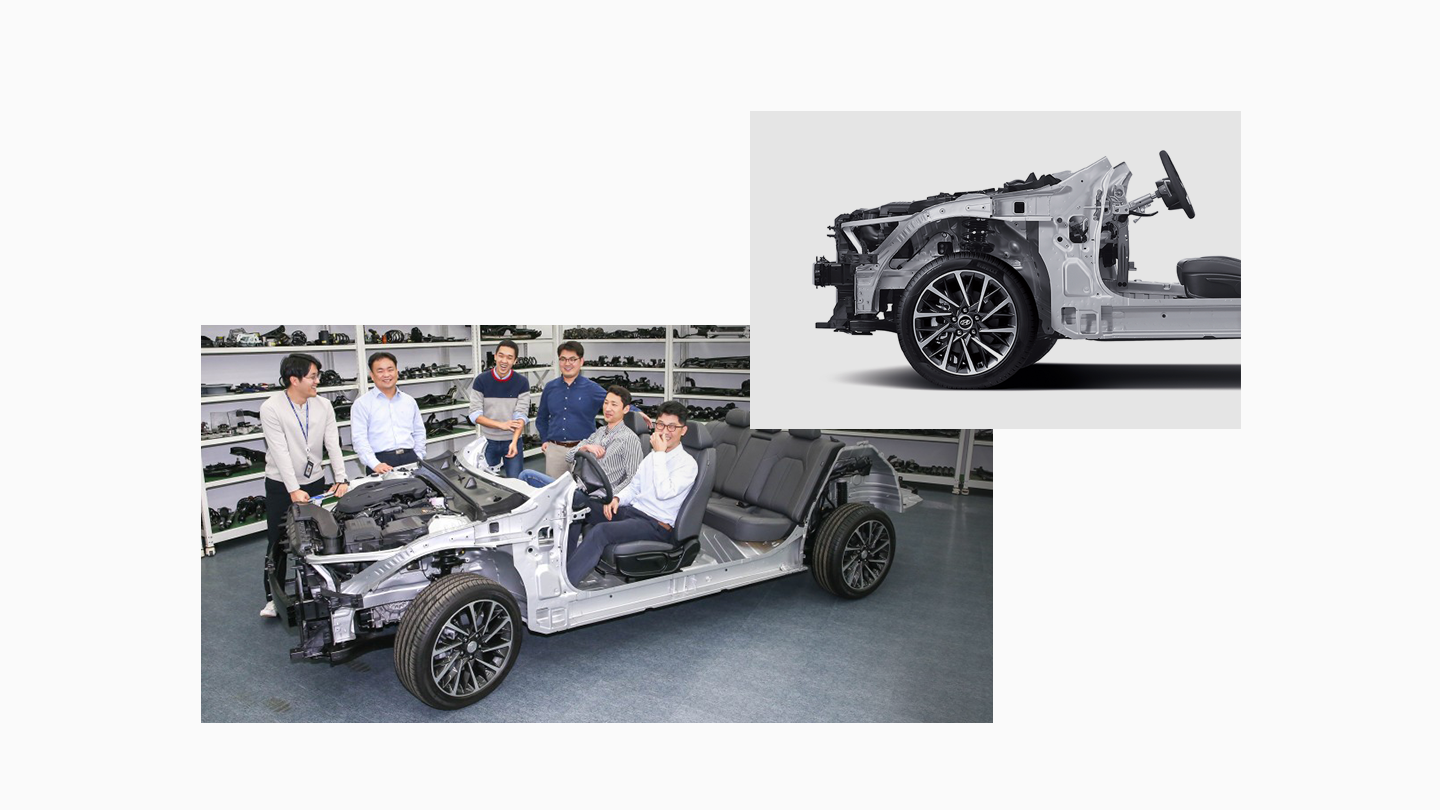
A well-developed platform can be an amazing canvas upon which an automobile is created but developing such a platform demands a great deal of effort and time. Platform development team at Hyundai Motor Group is proud to put forth a product of countless hours of intense, inspired work. Get behind the steering wheel of the all-new AVANTE and all-new TUCSON which features 3rd Generation Platform. It doesn’t take a seasoned driver to notice a difference.